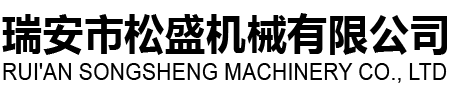
The inflation method can also be used to prepare biaxially oriented films. As long as the temperature is appropriate, the inflation ratio and traction ratio are appropriate, the bidirectional orientation can be roughly the same. If the drawing speed is too fast, the same blowing ratio may differ too much, and the longitudinal and transverse differences may be too large. The result is low transverse strength and easy breakage, just like the process of producing membrane fibers through uniaxial stretching. The prevention method is to appropriately reduce the traction speed to match the blowing ratio; Increase the airflow of the air ring to rapidly cool the blowing film and avoid stretching and orientation under high temperature and high elasticity conditions.
How to control the temperature of the blown film machine heater reasonably
Release date:2025/6/25 1:54:00 Number of clicks:26 次 news source:
Low pressure polyethylene hPPE adopts high-pressure polyethylene LLDPE mixture. Low voltage materials account for about 80%. The greater the pressure, the greater the tension. The disadvantage is that there is no stiffness, and too much can cause the blown film to swing back and forth, the edges of the blown film to be uneven, and even unable to blow in the end.
Firstly, it is preheated by the first, second, and third zones of the heater. The first area should be lower, usually around 170 degrees, while the other areas are around 200 degrees. If the temperature is high, the material cannot be transported out of the rod and may even burn and discolor. Next are four aspects, namely three stages. The purpose of placing a 60-160 mesh filter in the three-way valve is to prevent impurities from entering Zone 5. The larger the mesh, the thinner the screen, and the thinner the thin film that can be blown, including its transparency, feel, smoothness, tension, etc. However, too much or too thin will prevent the material from passing through, and too much will prevent it from being blown out. Generally, 3-5 pieces are recommended, and the thickness should be determined according to the requirements.
After blowing air into the air hole of the membrane head, add the air to the middle of the circular membrane, and the membrane will be in a straight line upwards. The size of the plastic bag is controlled by how much air is blown in, and then stabilized by a film stabilizer. The thickness is controlled by the engine speed and traction force. It can be understood that the faster the host speed, the faster the feed rate, and the thicker the oil film; On the contrary, the faster the traction, the thinner the oil film, which is the most important link.
When blowing low-density polyethylene (LDPE) film, the extrusion temperature is generally controlled between 160 ℃ and 170 ℃. It is necessary to ensure that the die temperature is uniform. If the extrusion temperature is too high, the resin is prone to decomposition and the film is fragile, especially when the longitudinal tensile strength is significantly reduced; The temperature is too low, the resin plasticization is poor, and it cannot expand and stretch smoothly. The film has low tensile strength, poor surface gloss and transparency, and even patterns such as wood rings and unmelted nuclei (fish eyes).
扫描二维码分享到微信